Indonesia Furniture Manufacturers - Truths
Indonesia Furniture Manufacturers - Truths
Blog Article
Some Known Facts About Indonesia Furniture Manufacturers.
Table of ContentsLittle Known Questions About Indonesia Furniture Manufacturers.The 6-Minute Rule for Indonesia Furniture ManufacturersGet This Report on Indonesia Furniture ManufacturersThe 5-Minute Rule for Indonesia Furniture ManufacturersThe 5-Minute Rule for Indonesia Furniture Manufacturers
There are some disadvantages to buying from a furniture producer. For one, you may need to wait longer to get your furnishings since it's being tailored. Furthermore, you may not have the ability to see or touch the item prior to you buy it. A furniture store is a company that markets furnishings made by numerous makers.When you purchase from a furniture merchant, you're buying a piece of furniture that's currently been made and prepares to be delivered to your home. Among the advantages of purchasing from a furnishings store is that you can typically see and touch the product prior to you get it.
At BH Furniture, we believe in setting brand-new requirements for excellence in the manufacturing of industrial furniture - Indonesia furniture manufacturers. Our commitment to technology has actually led us to embrace advanced automation modern technology, changing the method we manufacture furnishings and driving us to the leading edge of the market. Gone are the days of manual work controling the manufacturing floor
Our machinery functions seamlessly, guided by the accurate parameters established by our competent engineers, guaranteeing consistently premium output. Claim goodbye to manufacturing hold-ups and overtime costs. Our automated systems operate relentlessly, 24/7, guaranteeing a consistent and uninterrupted workflow. This indicates we not just meet however go beyond delivery due dates, supplying our customers with a level of dependability that typical production methods just can not match.
Not known Factual Statements About Indonesia Furniture Manufacturers
Our manufacturing ability has risen, permitting us to fulfill the needs of even the largest tasks without endangering on quality. As your partner in commercial furnishings options, we can effortlessly scale our output to accommodate your demands, no issue the range. While conventional production counts greatly on hands-on labor, our automated systems have considerably reduced our dependence on a huge workforce.
Furnishings manufacturing is a complex procedure that entails different stages, from designing and product option to manufacturing and assembly. At each stage, there is a possibility of issues or mistakes that can compromise the quality of the final product. To ensure that furniture is of top quality, furnishings suppliers implement top quality control processes to identify and fix any type of issues that might occur throughout manufacturing.
The inspection procedure ought to cover various elements, such as assembly, finish, colour, style, packaging, labelling, and marking. By carrying out a strenuous examination procedure, suppliers can ensure their products meet the needed high quality, safety, and durability demands. They additionally provide the versatility to address issues and make modifications prior to finishing the final item.
Furniture quality standards are sets of guidelines and demands for furniture manufacturing. They define the required quality level of additional reading furniture production and cover aspects such as safety and security, durability, strength, and environmental influence.
How Indonesia Furniture Manufacturers can Save You Time, Stress, and Money.

To guarantee their furniture items can withstand various climate elements, consisting of sunlight, rain, snow, and wind, suppliers need to think about internationally identified criteria that make up evaluations and screening. Here are a few of the requirements to remember: ASTM F1561-03 is a worldwide standard established by the American Area of the International Association for Testing Products (ASTM).
UL 962 is an international security standard established by Underwriters Laboratories (UL), an independent global supply security solutions company. The basic uses to family and commercial furnishings, consisting of outside furniture.
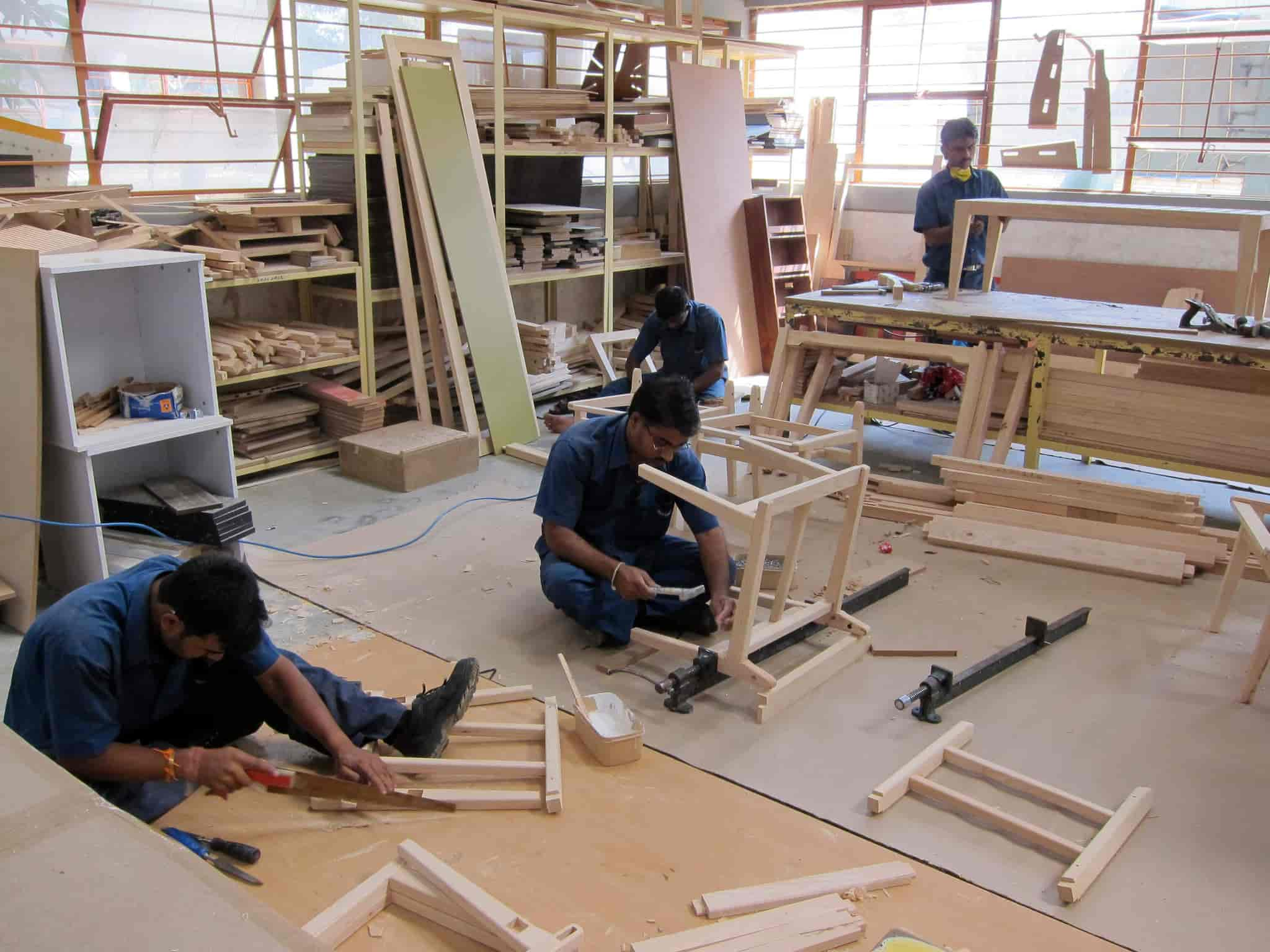
The 10-Second Trick For Indonesia Furniture Manufacturers
It aids to identify flaws in the furnishings and examine its efficiency and compliance with the needed high quality criteria. Here are the steps for performing lab screening for furnishings: Suppliers helpful hints collect samples of furnishings parts that call for testing. These samples typically stand for the different kinds of furniture that they create.
This may include a mix of various tests, consisting of strength testing, durability testing, safety testing, and environmental impact screening. The samples are after that examined for different quality parameters, such as stamina, resilience, safety, and ecological influence. The outcomes are after that evaluated to identify whether the items satisfy the needed high quality requirements.

Generally, every retail shop furnishings is various. Layouts meeting client comfort Taking full advantage of area use in storage space, display screen, footfall, guest seating and walkways Making sure simplicity of accessibility to products for trials and purchase Designing modular furniture that is easy to move and refit Satisfying security requirements of clients A fast TAT from style to production and setup with marginal mistakes can assist attend to the above worries.
Little Known Questions About Indonesia Furniture Manufacturers.
Additionally, a developer can understand the marketplace patterns and be prepared with innovative layouts in advance. Check out below: Exactly How DriveWorks Helps You to Minimize Lead Time in Production Developers often need to alter the sizes and shapes of furnishings at a minute's notice. These may have different aesthetic and practical demands like front workdesk, and maintenance desk that differ in dimensions.
Boosts product top quality and lowers scrap. Field instruction papers along with quantity launches are additionally generated for retail shop Continue furniture installations. Layout iterations and problems are lowered, and the shop floor can begin manufacturing on the day of sales.
It is a highly competitive market, with businesses making every effort to maintain up with transforming customer demands and the latest technical trends. Today's consumers are extra likely to favor furnishings that is personalized and made with lasting materials.
Report this page